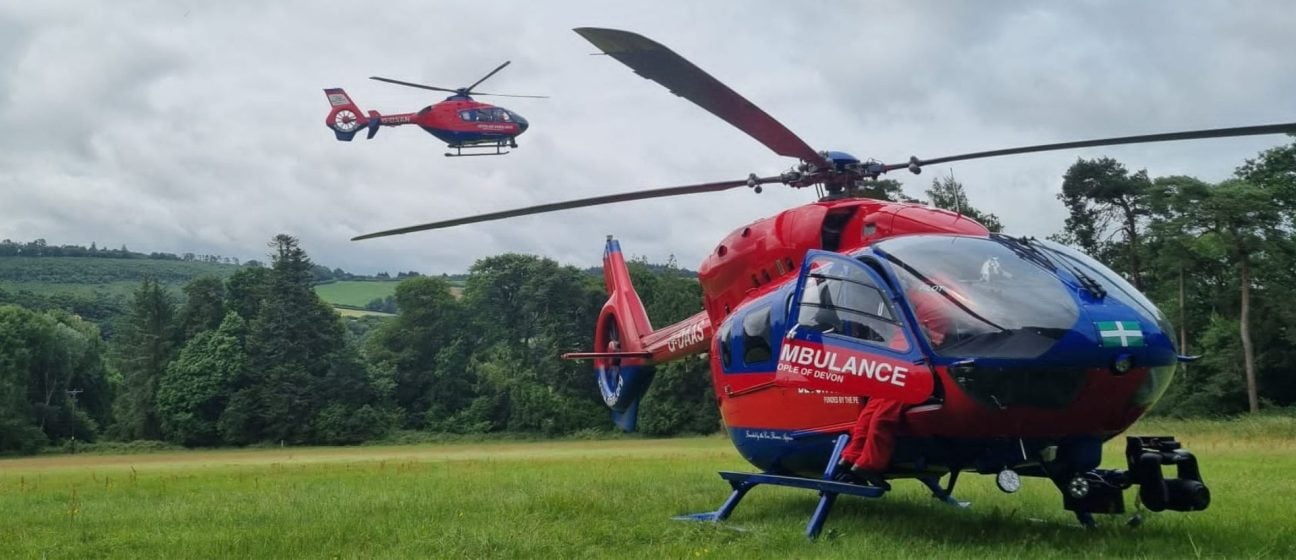
Michael Snowden, Head of Continuing Airworthiness Manager in the Flight Operations team, focuses on one such essential item of maintenance: repairing a defective light bulb.
We’re often asked questions about specific aspects of our aircraft. Michael Snowden, Continuing Airworthiness Manager in the Flight Operations team, focuses on one such essential item of maintenance: repairing a defective light bulb.
An aircraft is an expensive asset and essential to our lifesaving service. Our engineers ensure both of our aircraft are safe for flying through regular maintenance checks and repairs.
For example, one such defect might be that the landing light bulb cannot be turned off via the usual switch and instead the only way to turn it off is to pull the circuit breaker.
The cause of this defect is that one of the relays in the electrical circuit is faulty, so when the switch is turned to the off position, the relay doesn’t allow power to pass through it to remove the electrical power to the bulb.
So, how easy is it to replace the relay? Well, it took two engineers, 5 and a half hours together to gain access to the relay, replace the faulty part, then perform functional tests of the disturbed parts ahead of testing the landing light.
Why did it take so long for what initially might appear to be a simple/easy task? The relay is located inside the overhead panel which is positioned in the roof of the cockpit. From the images below you can see why this is not as straightforward as repairing a typical light bulb!
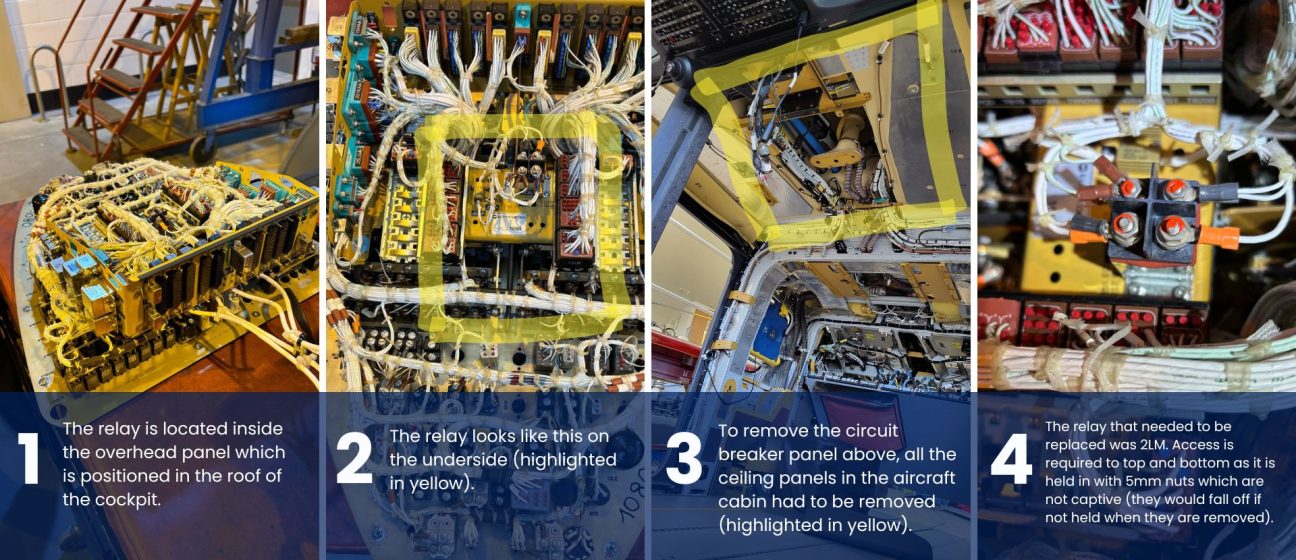
Once the relay was replaced, all the removed parts were re-fitted, functional tests carried out. Prior to releasing the aircraft back to service, the engineers completed their favorite part of the job: the paperwork!